Control valves are the unsung heroes of industrial processes, silently regulating flows in harsh environments. Yet, 43% of premature valve failures stem from preventable issues like improper maintenance or cavitation (2023 Valve Industry Report). By implementing these 7 data-backed strategies – including specialized fluorine-lined valve applications – you can boost valve service life by 50% or more while cutting replacement costs.
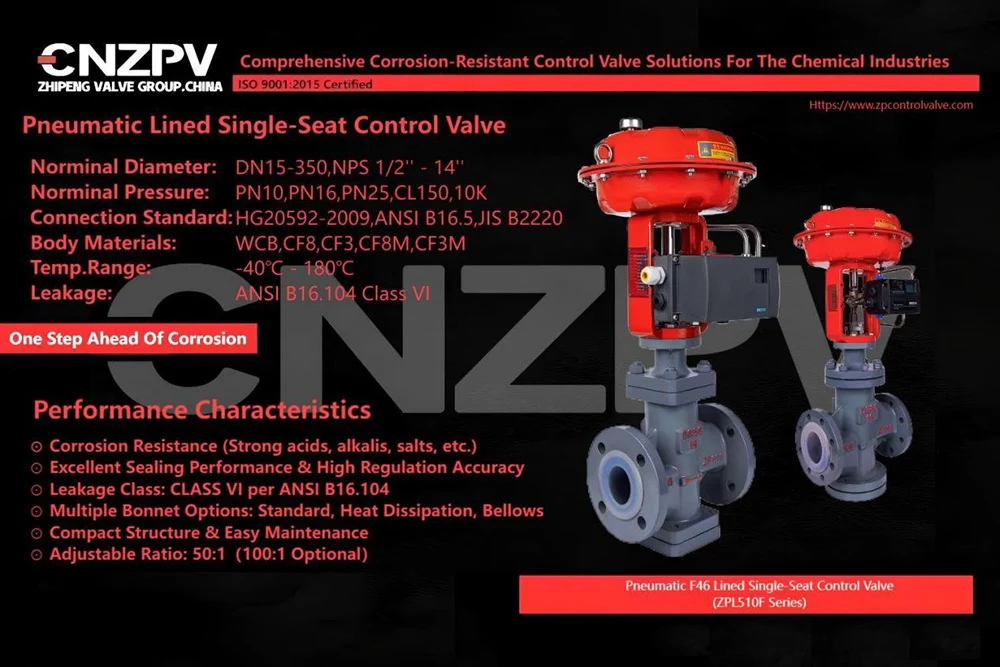
1. Precision Maintenance: Beyond Basic Checks
Why it matters: A study by the Fluid Controls Institute found valves with scheduled maintenance last 2.3x longer.
Actionable Protocol:
For fluorine-lined valves: Conduct quarterly PTFE liner thickness checks via ultrasonic testing
Use compatible lubricants (silicone-based for fluoropolymer components)
Special attention to bolt torque (PTFE gaskets require retorquing after 48hrs of service)
2. Fluorine-Lined Valves: The Corrosion Solution
Game-Changing Advantage: Fluoropolymer-lined valves demonstrate 97% survival rate after 5 years in sulfuric acid service (Garlock Case Study).
Key Benefits:
✔ Chemical Immunity: Withstands pH 0-14, including aqua regia and chlorine gas
✔ Temperature Range: -200°C to +180°C with PFA liners
✔ Cost Efficiency: 60% lighter than solid alloy valves, reducing actuator load
✔ Non-Stick Surface: Prevents scaling and particulate buildup
Liner Material Comparison:
Material | Max Temp | Best For | Service Life |
PTFE | 150°C | General acids | 5-7 years |
PFA | 180°C | Ultra-pure processes | 8-10 years |
ETFE | 150°C | Oxidizing agents | 6-8 years |
3. Combatting the Silent Killers: Cavitation & Flashing
The Cost: Unchecked cavitation can erode valve trim 10x faster than normal wear.
Fluorine-Lined Valve Solutions:
Lined valves inherently resist cavitation damage due to elastomeric backing
PFA-lined trims maintain smooth surface finish (Ra <0.8μm) to prevent nucleation
4. Material Science Approach
Breakthrough: Vortex-shedding resistant alloys like Duplex 2205 extend trim life by 40% in slurry services.
Fluorine-Lined Valve Enhancement:
Hybrid designs with alloy bodies + fluoropolymer liners combine structural strength with chemical resistance
Electropolished metallic components prevent liner abrasion
5. Smart Valve Analytics
IoT Advantage: Plants with IIoT-enabled valves report 72% fewer unplanned shutdowns (ABB Whitepaper).
Fluorine-Lined Valve Monitoring:
– Dielectric sensors detect liner degradation before leaks occur
– Temperature mapping ensures liner stays within Tg (glass transition) limits
6. Installation Mastery
Critical Error: 68% of field failures originate from improper installation (Emerson Case Study).
Fluorine-Lined Valve Specifics:
✓ Always use flange spreaders – never pry liners during installation
✓ Pre-compress PTFE gaskets at 50°C above operating temp
✓ Avoid sharp bends – maintain 5D radius for lined piping
7. Failure Mode Clinics
Transformative Practice: Tear-down analysis reveals:
Fluorine-Lined Valve Findings:
90% of failures occur at unlined components (stems, bolts)
Properly installed liners typically outlast valve bodies
Most common issue: Thermal cycling beyond liner specs
Your Next Steps
Free Lined Valve Assessment] Our engineers use borescopes and dielectric testing to evaluate liner condition
Download Chemical Resistance Guide] Interactive material selection tool for aggressive media